The wastewater treatment plant (WWTP), Arnhem Zuid, is one of 31 WWTPs allocated to the Water Board of Rivierenland region in the Netherlands. The plant has a designed capacity of 206,000 p.e.. The actual load in 2021 was 327,000 p.e. and a hydraulic throughput of 6,400 m3/hour. Phosphorus is treated biologically with a denitrification stage.
Arnhem achieves more sustainable operations through data-driven chemical treatment
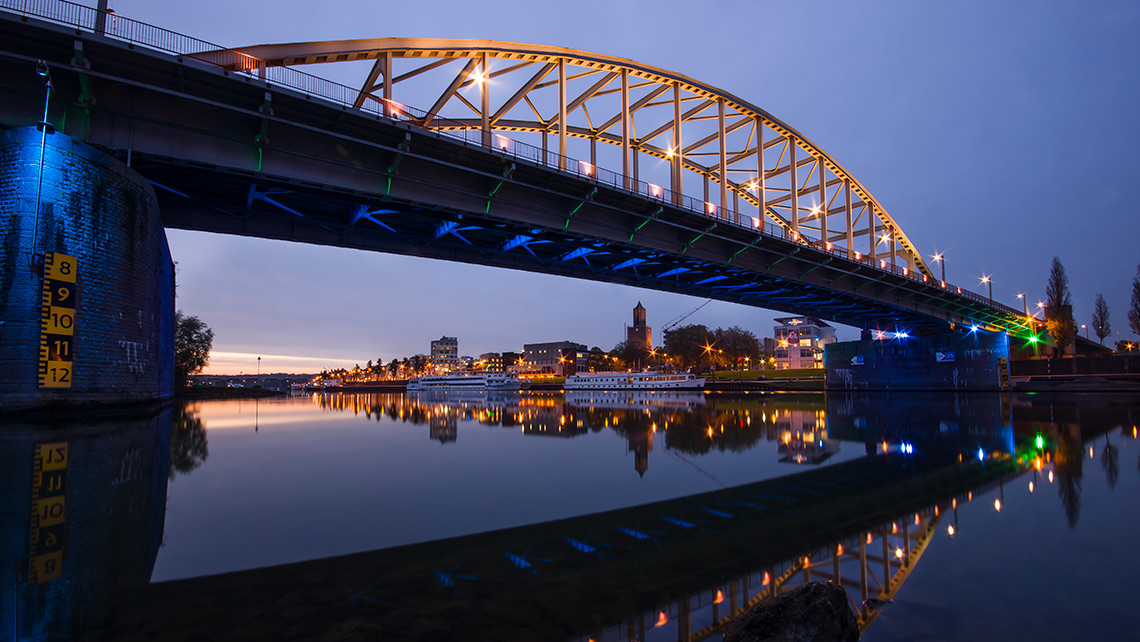
Challenges with polymer consumption and centrate quality
In order for the Arnhem Zuid WWTP to operate more efficiently, one key parameter was to monitor and control the polymer consumption for the digested sludge dewatering process. The sludge is treated in an anaerobic digester, generating biogas, which is used to supply energy for the wastewater treatment process.
The sludge is dewatered using two centrifuges with polymers to maximize the dry solids (DS) level. In 2021, both centrifuges delivered an average DS sludge content of 21%. However, during certain periods there was a challenge with insufficient centrate quality, sometimes even with a dark color. Together with Kemira, the operators at Arnhem Zuid investigated how an improvement could be achieved.
The following Key Performance Indicators (KPIs) were identified by Rivierenland Water Board
- Centrate quality
- DS of dewatered sludge
- Polymer consumption
- Total Cost of Operation
- Process transparency
Getting the chemistry right
By the end of 2021, Kemira started testing a more suitable polymer, in combination with an iron-based coagulant. The newly developed polymer Kemira Superfloc® SD-7083 proved to be the best-performing polymer. The combination between Ferric Sulfate (PIX-113) and Superfloc® SD-7083 lead to significant process performance improvements and allowed for much more efficient chemical dosing.
Technical achievements
- Higher-sludge dry solids
- Clean centrate
- Lower solids recirculation through centrate back to the inlet of the WWTP
Economical benefits
- Lower Total Cost of Operation: savings achieved € 150,000/year
Sustainability benefits
- Lower carbon footprint due to reduced polymer consumption (-20 tons CO2 equivalent based on chemical use)
- -7% reduction in sludge transportation (truck rides)
In the beginning of 2022, Kemira’s digital solution for automated chemical dosing, Kemira KemConnect™ SD, was installed for one of the centrifuges to reinforce the improved chemical treatment process. During this period, the centrifuge equipped with the data-driven KemConnect™ solution continuously outperformed the other centrifuge which was controlled by the supervisory control and data acquisition (SCADA) system.
Main KPIs before and after
Situation in 2021 with previous product Average for the 2 centrifuges |
Situation in 2022 Centrifuge 1 equipped with KemConnect™ SD |
Situation in 2022 Centrifuge 2 controlled by SCADA system |
Sludge DS 21.0% |
Sludge DS 21.5% |
Sludge DS 20.0% |
Polymer dosage rate 60 kg/ton DS
|
Superfloc® SD-7083 dosage rate 28 kg/ton DS (expressed as kg product) Ferric sulfate dosage rate 2 l/m3 incoming sludge |
Superfloc® SD-7083 dosage rate 45 kg/ton DS (expressed as kg product) No ferric sulfate dosed |
Black centrate |
Clear centrate |
Clear centrate |
When comparing the economical advantages, calculations show that the average total costs for the sludge treatment are approximately € 60 lower per ton of DS using KemConnect™ SD. With an average sludge production of 2,500 ton DS/year, this results in an annual net savings of € 150,000.
One of the biggest advantages is that we are now monitoring and optimizing 24-7.
“The KemConnect™ platform allows us to control and monitor actual total costs for sludge treatment, next to other parameters we obtain during the treatment. This has resulted in much clearer insight into the dewatering process. One of the biggest advantages is that we are now monitoring and optimizing 24-7. Additionally, the automated monitoring and ordering of chemicals is a big plus for the continuation of the sludge treatment process in the current chemical market with supply shortages.” says Gustaaf Speller, Residuals manager, Technical Installations Operations from Waterboard Rivierenland.
For more information, please contact
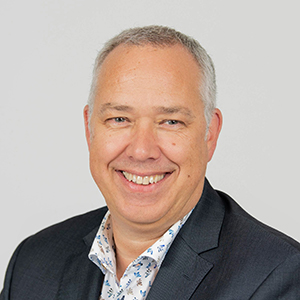