The picturesque Åland Islands, located in the Baltic Sea midway between the south coasts of Finland and Sweden, are a popular tourist destination. The administrative capital of Mariehamn is home to the Lotsbroverket wastewater treatment plant (WWTP), which serves a population equivalent of 30,000 from its underground coastal location. As well as processing municipal wastewater, the plant also serves a large industrial food manufacturing plant nearby.
The plant’s treatment process comprises:
- Sand traps at incoming flow
- Pre-sedimentation
- Biological filtration
- Sedimentation
- Flotation
Seeking a solution to a biological problem
The plant had been facing challenges with its wastewater pre-treatment processes, specifically the biological treatment. The large variations in total suspended solids (TSS) and biological oxygen demand (BOD) in the outflow from the primary treatment step were causing knock-on effects in the biological treatment, including excessive energy costs related to aeration.
“Mariehamn Municipality has been a Kemira customer for a long time,” explains Mohammed Khaytan, Advanced water treatment Manager, Kemira Nordics. “The customer’s interest in KemConnect PT started when a representative from the plant attended a webinar we held about the solution in late 2021. After that, the customer got in touch to find out more and we proposed some lab tests to demonstrate the value of the solution.”
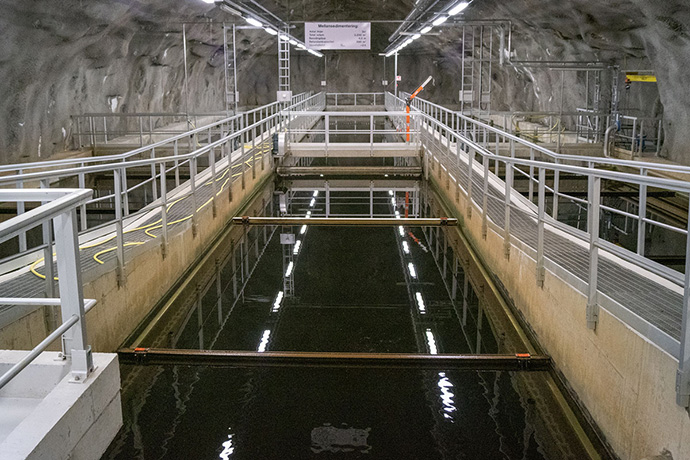
Lotsbroverket wastewater treatment plant in Mariehamn.
An automated solution to optimize pre-treatment
Kemira KemConnect PT is an automated solution to optimize the chemical pre-treatment of wastewater. It is a data-driven approach designed to maximize energy savings and energy production while maintaining a consistent, stable treatment process. The solution measures flow, turbidity, and suspended solids in the influent wastewater, as well as ammonium, phosphate, COD, and nitrate and oxidation reduction potential in the nitrification/denitrification process. It also includes feedback input loops from aeration energy and biogas production. Intelligent algorithms are used to calculate the optimal chemical dosage for the desired outcome based on the existing conditions.
“KemConnect PT is an excellent option for plants where there is limited space or capital investment available for major plant expansion,” says Bengt Hansen, Application Development Manager at Kemira. “We can make a big impact in a very small footprint, which made the solution ideal for Lotsbroverket because of its underground coastal location. Essentially, KemConnect PT allows us to tailor the wastewater coming from the pre-treatment step according to the customer’s exact requirements and the design of the plant. By monitoring what is happening in the primary treatment step we can simulate what will happen two hours ahead and control and optimize the chemical dosing process accordingly.”
KemConnect PT allows us to tailor the wastewater coming from the pre-treatment step according to the customer’s exact requirements and the design of the plant.
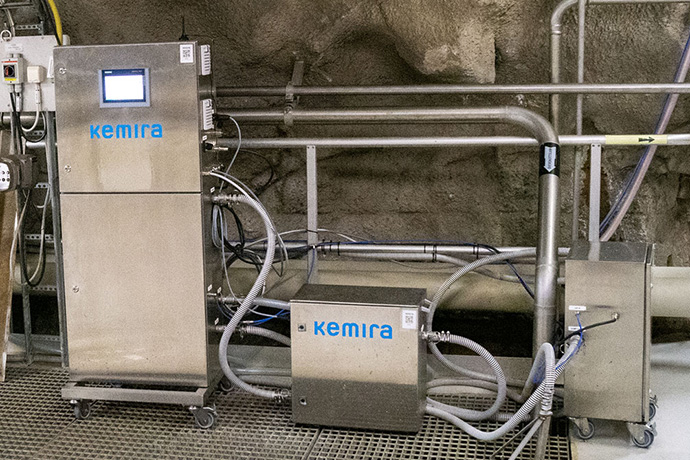
KemConnect PT unit at Lotsbroverket WWTP.
KPIs set the measure of success
After initial discussions with Kemira’s experts to map out the plant’s needs and quantify the value that KemConnect PT could deliver, the customer was keen to take things a step further with jar testing conducted by Kemira experts. These pilot-scale laboratory tests simulate coagulation or flocculation with different chemical doses to estimate the minimum effective dose required to achieve certain water quality goals. “The results of the tests convinced the customer to trial KemConnect PT for three to six months,” explains Khaytan.
The customer set out the following KPIs for the trial:
- Bring the ratio of carbon to nitrogen to phosphorus in wastewater closer to 100:5:1 before the biological step
- Achieve 125 mg/l TSS after primary settling
- Increase biogas production by 9%
- Reduce iron-based coagulant consumption by 20%
- Reduce overall costs of the treatment process (energy, chemical consumption, etc.)
During the initial trials Kemira’s hands-on approach ensured that everyone was kept up to date on the progress of the project. “We held meetings every other week to go over the results so far and answer any questions or concerns the customer had,” says Khaytan. “This is a key element in our way of working. These regular checkpoints and our open, transparent dialogue helped the customer feel comfortable and kept them fully informed at all times. After the trial we were able to demonstrate that the KPIs had been achieved, so the customer agreed to implement KemConnect PT full time.”
Eye-opening energy, chemical, and sludge disposal costs
The KemConnect implementation at Lotsbroverket has been a resounding success on all fronts, as the numbers demonstrate. “Firstly, the customer is now using up to 55% less chemicals to achieve their wastewater quality objectives, which translates into significant cost savings,” Khaytan points out. “The 26% increase in TSS means more primary sludge to the digester, which reduces the organic load. As a result they are using 6% less energy overall, which is not only a considerable monetary saving but also reduces the plant’s carbon footprint. The optimized treatment process has also increased nitrogen removal by 6% and helped to cut sludge disposal costs by 10%.”
The customer is now using 55% less ferric sulfate to achieve their wastewater quality objectives, which translates into big cost savings.
“Before implementing KemConnect PT we had limited visibility over our primary treatment process and the knock-on effects of the issues we were having with variable TSS and BOD. The solution has not only solved the challenges we were facing but has also opened our eyes to what is happening in our processes and where we can improve. We also appreciate the fact that while Kemira is very hands-on with their support and guidance, the KemConnect PT solution on site is very hands off and requires almost no time and effort from us to maintain.” says Tomas Mörn, Plant Manager, Lotsbroverket WWTP.