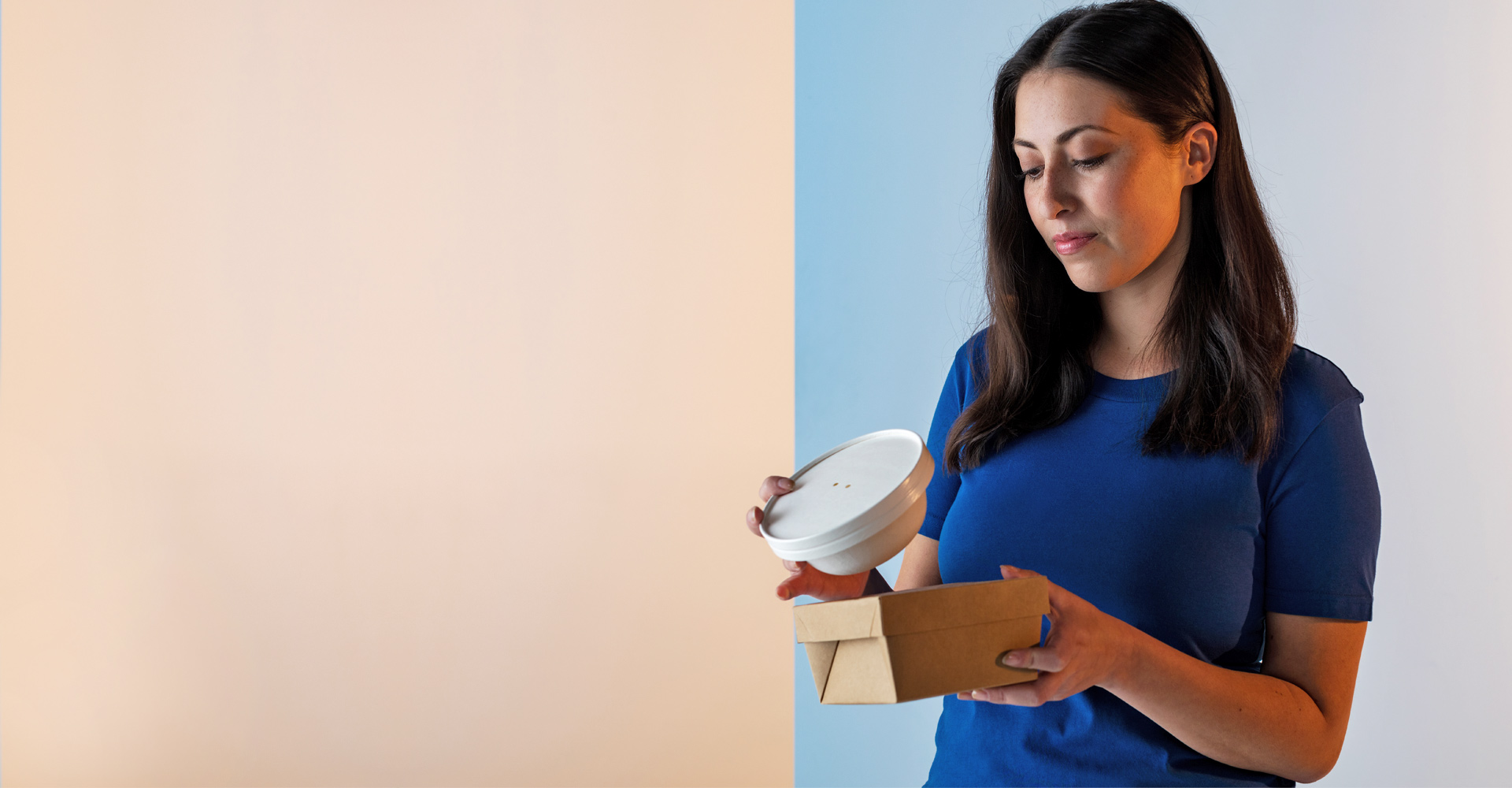
It’s time to pay attention to the unseen
See the invisible
Enabling recyclable, functional, and safe food packaging
Chemistry is the invisible enabler for recyclable, functional, and safe fiber-based food packaging. With our expertise, application know-how, and chemicals, we are an essential part of the value chain that is working together to find future-proof solutions to global sustainability and resource efficiency challenges that impact packaging.
Without chemistry, paper or board could not be turned into fit-for-purpose packaging. The packaging material would not have the required stiffness, strength, convertibility, or hydrophobicity; it would neither protect the product nor be hygienic and safe to use; it would not withstand being shipped or carried around.
It’s time to pay attention to the unseen.
Board & Packaging
Hygiene and product safety
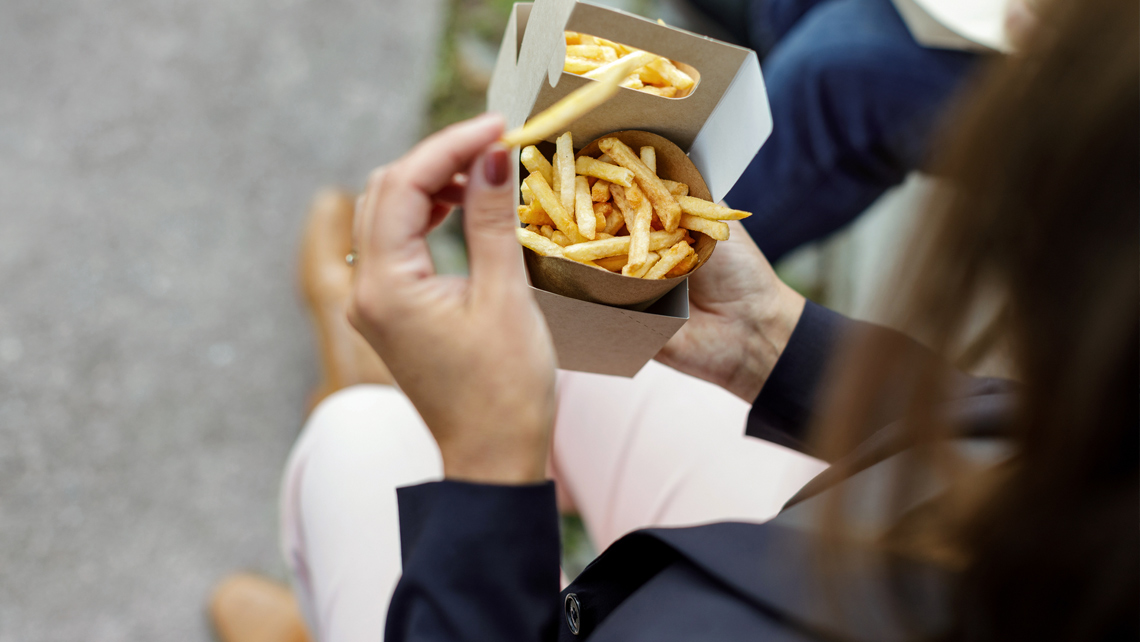
Liquid resistance, printability and convertibility
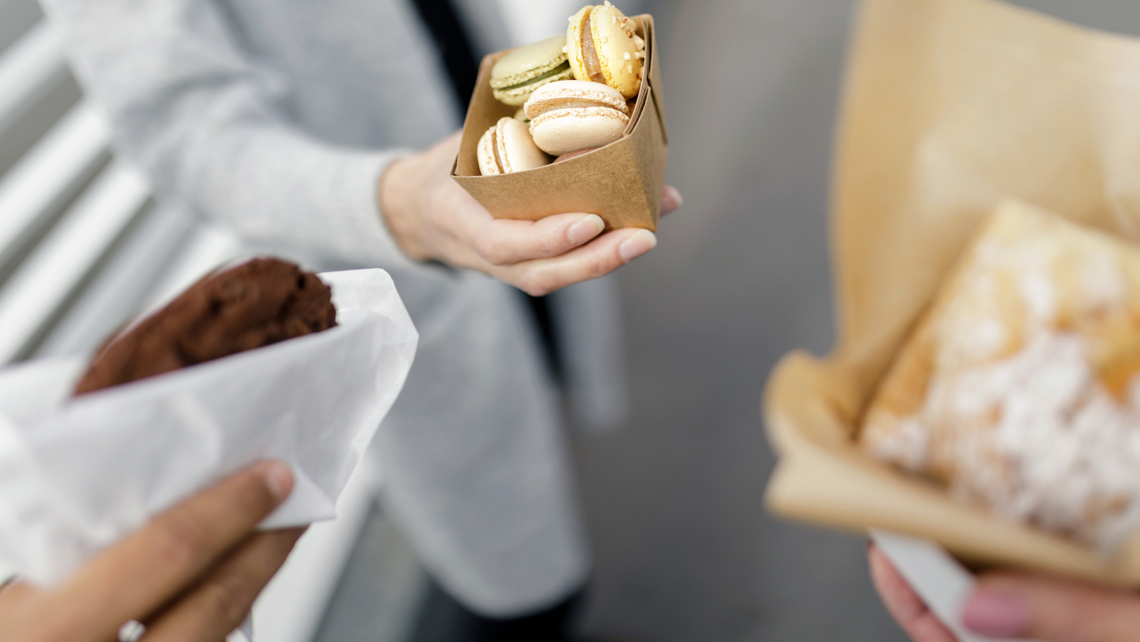
Lightweighting and strength
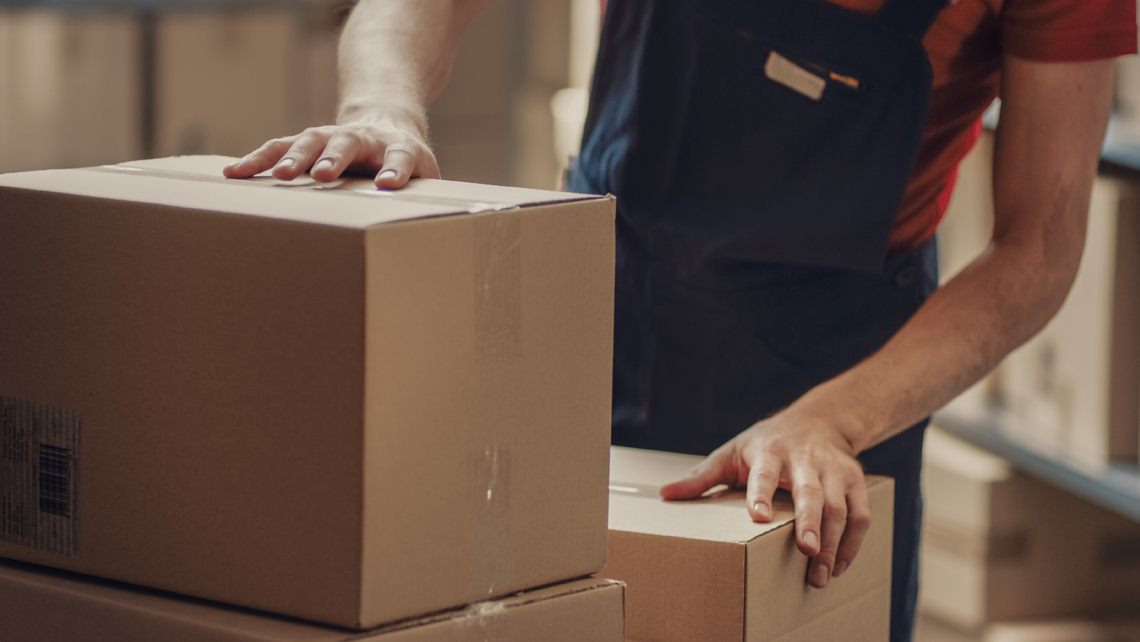
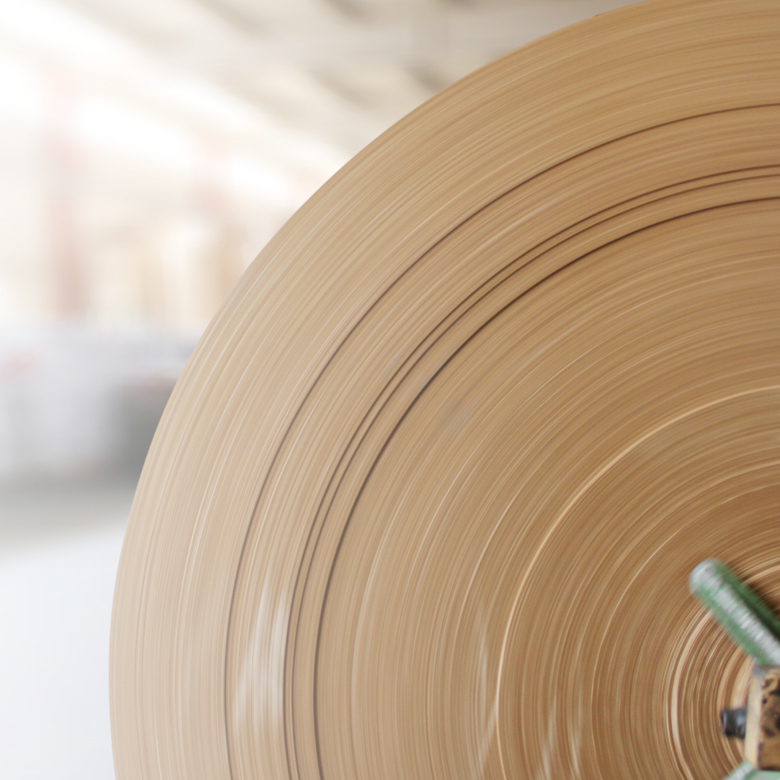