Miami-Dade South operates one of the largest wastewater treatment plants in the state of Florida and it utilizes a conventional activated sludge process, dewatering the plant’s anaerobically digested sludge via four Sharples centrifuges. Wastewater flow at the plant averages a massive 100 million gallons daily, with sludge flow to the dewatering operation averaging 600 gallons per minute. It was clear to Kemira that such a large capacity plant would benefit from their KemConnect™ real-time process monitoring and performance optimization solution.
Facing a big challenge
Struvite formation is a common challenge for wastewater treatment plants that utilize anaerobic sludge digestion. At the Miami-Dade plant, heavy struvite build-up had continued for years and it was starting to cost them more time and money. It impeded their dewatering operation and forced them to clean their systems on a weekly basis. This was time-consuming, resource hungry, and caused unnecessary downtime. Worse, the struvite was also damaging their centrifuges, leading to frequent repairs and yet more downtime. It was such a serious problem that they knew they had to do something about it. The answer came from Kemira and KemConnect.
Richard Waterous, Senior Specialist in AWT Sales at Kemira initiated the discussion to offer the right solution. “We were asked to solve this problem based on our success with eliminating struvite at the Miami-Dade Central plant,” he explains.
It was a home run!
There was no struvite to be seen.
Richard Waterous
Working together for a customized solution
“Our approach was not only to apply the right chemical but to work with the customer for a complete value-adding solution,” explains Tafadzwa “Tee” Mariga, who works as a Sr Sales Manager at Kemira. Kemira’s team recognized quickly that the amount of ortho-phosphorus in the sludge needed to be decreased. Utilizing wastewater treatment expertise, the right solution was identified through laboratory testing.
The solution was based on Kemira’s enhanced solids management program, powered by KemConnect real-time process monitoring and performance optimization. “The program is unique in the market. It combines our expertise, chemistry, and smart technology,” Tee explains. “It can be customized to fit the customer’s primary needs, such as struvite control or drier cake solids or low dewatering costs per dry ton of sludge processed.”
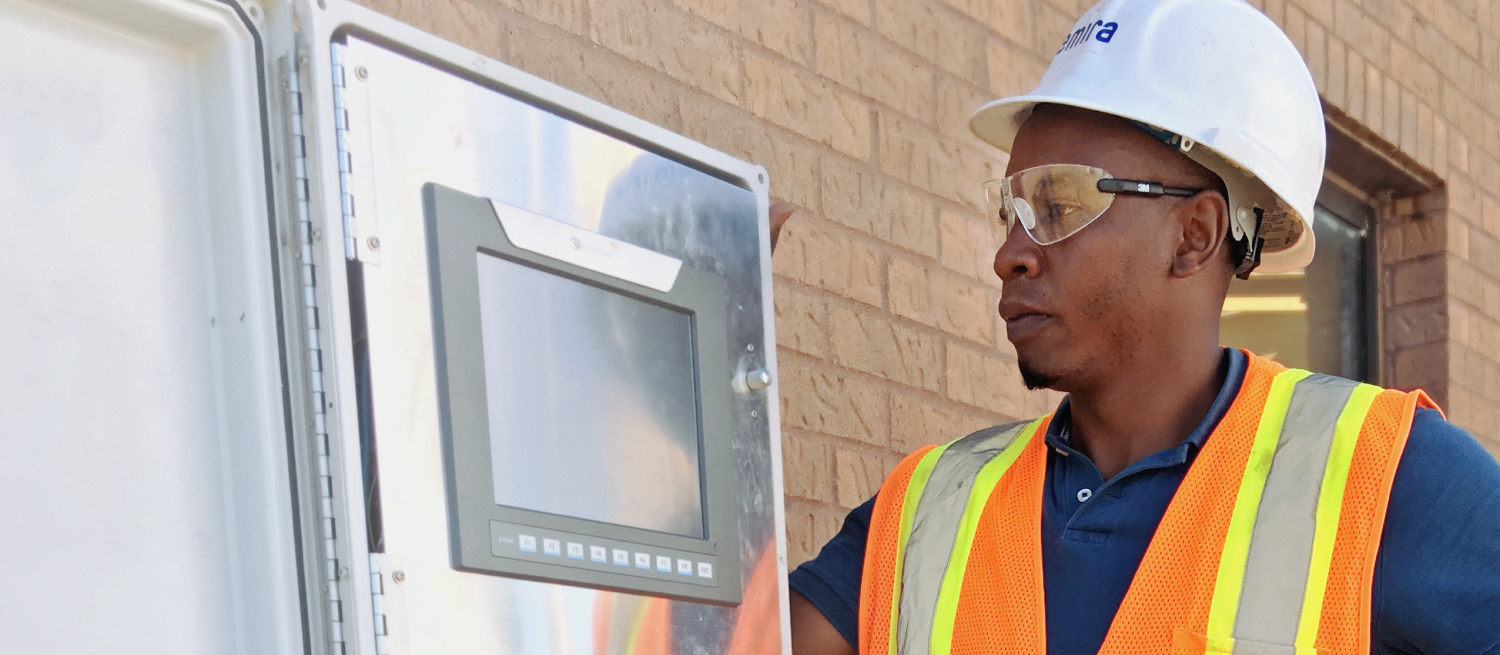
We eliminated the struvite problem immediately
Only a week after being introduced, the results became clear when the plant’s system was opened for a weekly washing. “It was a home run! There was no struvite to be seen,” describes Richard. “With our laboratory testing and methodological approach, we can offer a very precise recommendation for the needs of each customer,” he continues.
In addition to struvite elimination, Miami-Dade South is also reaping other benefits, including significant cost savings in man-hours needed for maintenance activities. Since its implementation, the solution has provided the plant with an extensive reduction in polymer demand, with the centrate capture rate increasing from 87% to 99%. The amount of cake solids also increased.
Kemira has since continued working closely with the customer to provide solutions to other issues at the plant.
The benefits for Miami-Dade continue to grow
- Elimination of struvite formation
- Reduced maintenance costs
- Cost savings as a result of 50% reduction in polymer demand
- Estimated process cost savings of about 10%
- Optimized real-time control and performance monitoring
- Up to 4% total solids increase in cake solids
- Reduced odors
- Automated polymer feed system